Thermal Laser Epitaxy
We have proposed and are exploring a novel concept for the precise growth of ultraclean films and heterostructures: Thermal Laser Epitaxy (TLE). This concept combines the advantages of molecular beam epitaxy (MBE) and pulsed laser deposition (PLD) and overcomes the bottlenecks of both techniques. TLE uses CW-lasers (~1 μm wavelength) as heaters to evaporate elemental or compound source materials. Another laser (~10 μm wavelength) is used to heat the substrates.
The concept has been published in AIP Advances, Published online August 14 (2019).
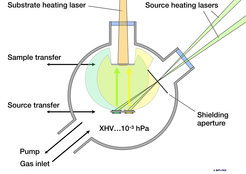
As shown schematically in Fig. 1, the local laser heating allows the use of freestanding solid sources, acting as their own crucibles even for materials that are liquid at the process temperature. The avoidance of crucibles or Knudsen cells cuts impurities and enhances the performance of the whole system by eliminating all problems associated with contamination or different thermal expansion between crucible and source material. As shown, the source heating lasers are focused through shielding apertures to protect the entrance windows from detrimental coating by the evaporated fluxes. Both the sources and the substrates can be easily transferred in and out of the chamber, allowing for the rapid exploration of different compounds.
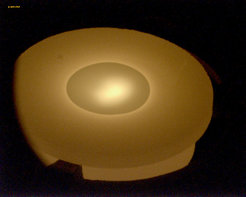
Figure 2 demonstrates the evaporation of silicon in a TLE chamber as an example. Due to the compact sizes of the sources, a short working distance is possible allowing for efficient usage of the source materials, because the deposition fluxes vary as 1/r² (r being the source-substrate distance). The deposition chamber is extremely simple in design consisting mainly of two laser windows and two mechanical holders for substrate and sources, respectively. The rapid heating and cooling provided by the lasers enable high-throughput and efficient operation. The composition of the background atmosphere and chamber pressure are limited only by the requirement that the mean free path of the evaporated species exceeds r. Due to the direct line-of-sight transfer of the material, the process and the equipment are scalable to large sizes.